Thermal management of battery-powered electric vehicles is important because it affects the performance, reliability, and stability of these vehicles. Optimal operating temperatures are important for the proper functioning of an electric vehicle's battery pack, electronic control system, and motor. When maintained at optimal temperature, it slows down the decay of the battery's charge, health, and capacity. Electronic controls and motors also work optimally at optimal temperatures. TKT HVAC began researching and designing Battery Thermal Management Systems (BTMS) in 2012. Our foundation is to optimize battery performance, extend its life, and increase energy efficiency.
1. Components of a thermal management system for electric vehicles
Battery Thermal Management
The performance, lifetime, and cost of battery packs and electric vehicles are directly related. At optimal temperatures, discharge power during starting and acceleration, charging capacity during regenerative braking, and battery health are all at their best. As temperatures rise, battery life, EV drivability, and economy all decline. Considering the overall thermal impact of batteries on electric vehicles, battery thermal management is critical.
Thermal management is especially important for lithium-ion batteries, where the reactivity of the lithium, nickel cobalt, graphite, and copper chemistries in the battery depends on its temperature. The ideal discharge temperature for lithium-ion batteries is 20 °C. Below this "comfortable" temperature, the charging/discharging efficiency of traction batteries decreases, and therefore the vehicle's range is reduced, as well as the battery's service life.
Therefore, at lower ambient temperatures, the battery must be quickly heated to operating temperature after the vehicle has been started. During driving, thermal management must control the temperature of the lithium-ion battery between 25 °C and a maximum of 45 °C to ensure that the battery delivers its full performance at high efficiency.
During fast charging, the optimum battery temperature is around 40 °C, because at this temperature the internal resistance of the lithium-ion battery is minimized, the battery charges particularly fast and the losses are low. In addition, the battery also heats up during charging. The thermal management system must remove this heat from the battery pack in time to ensure that the optimum charging temperature is maintained. If this temperature is exceeded, the charging current must be reduced to prevent irreversible aging of the battery.
.jpg)
Thermal Management of Motor Control Systems MCUs
The motor control system is responsible for controlling the motor. The motor control system MCU drives the motor according to the EV control system VCU control commands. The DC-DC converters, inverters, and control circuits in the motor control system MCU are susceptible to heat. During operation, the power switching devices generate heat loss and need to be cooled in time. If the heat is not managed properly, it may lead to control failures, component failures, and vehicle operational failures. Often the electronic control system is connected to the
electric vehicle's cooling system to maintain optimal temperatures.
Thermal management of electric motors
Since the wheels of an electric vehicle are driven by electric motors, the operating temperature of the motors is critical to the performance of the vehicle. As the load increases, so does the heat generated by the motor. To ensure the performance of the electric vehicle, the motor must be cooled.
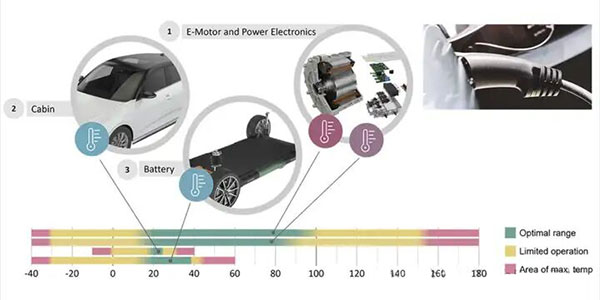
"Comfort" temperatures for individual components of electric vehicles
2. Typical Thermal Management System Architecture
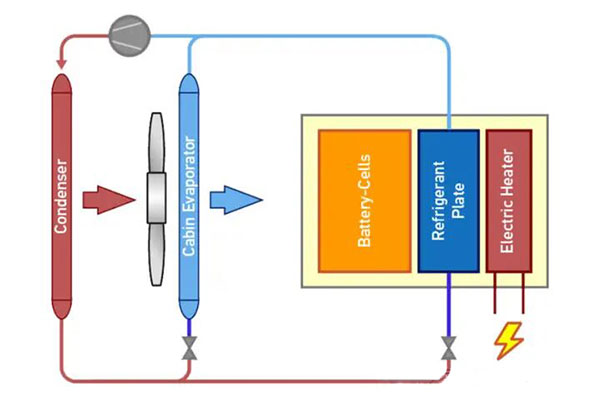
Thermal management architecture based on the refrigerant circuit (direct battery cooling)
The refrigerant-based system circuit consists of the following main components: condenser, evaporator, and battery cell (battery, cooling plate, and electric auxiliary heater). The heat-generating components are cooled mainly by the refrigerant circuit of the air conditioning system and the circuit temperature is controlled by valves and temperature sensors. This architecture is relatively simple, with only one cooling circuit, and the battery is cooled directly by the air conditioning circuit.
.jpg)
Thermal management architecture based on refrigerant and coolant circuits (indirect battery cooling)
The entire cooling system is subdivided into several circuits, each with a separate cooler, coolant pump, thermostat, and shut-off valve. The refrigerant circuit of the air conditioning system is also integrated with the coolant circuit via a special cooler Chiller. At low outdoor temperatures, a high-pressure heater heats up the coolant and keeps the battery working at a suitable operating temperature.
In order to fully utilize the performance and at the same time ensure the longest possible service life, the coolant temperature of the battery needs to be kept between approx. 15 and 30 degrees Celsius at all times. When the temperature is too low, the coolant is heated by an auxiliary high-pressure heater. When the temperature is too high, it is cooled by means of a low-temperature cooler. If this is not enough, the refrigerant from the air conditioning system flows through a heat exchanger, which further cools the coolant flowing through the cooler Chiller.
The coolant temperature of the motor and the electronic control system is maintained within a separate circuit (inner circuit in the diagram), which is controlled by a radiator to keep the coolant temperature no higher than 60 degrees Celsius at all times.
In summary, the thermal management system TMS for electric vehicles adapts to the temperature conditions outside and inside the electric vehicle, regulating the battery pack, electronic control, and motor to the optimal operating temperature.
3. Future Trends of Thermal Management Systems
Advances in Thermal Management Technology: PCM and GIHP
With the introduction of high-density batteries and fast chargers to the electric vehicle market, increasing the amount of heat generated by the battery pack, TMS will begin to use phase change materials (PCM) and gas injection heat pump (GIHP) systems to improve performance. PCM is primarily used to limit overheating, while GIHP is used to bring the battery temperature up to the proper operating temperature in cold weather conditions.
CAN communication support for easy TMS diagnostics?
The CAN bus is a message-based protocol for diagnosing and troubleshooting the most critical systems in a vehicle, depending on the configuration, and operates at speeds of up to 1 Mbit/s. High-speed CAN buses are becoming more and more integrated into automotive systems, and the BMS can send commands to the TMS over the CAN bus to ensure optimal battery operation, and the TMS can provide real-time feedback on system diagnostics to the BMS. BMS can send commands to TMS via CAN bus to ensure optimal battery operation, and TMS can provide real-time system diagnostic information to BMS.
4. Thermal Management System Challenges
The design of a battery thermal management system is very complex. Increasing power without compromising system performance and reliability is a major issue in the design of thermal management system components.
In liquid-cooled thermal management systems, there is a risk of leakage at the piping interface connections as the battery ages. In liquid-cooled systems, the cold plate corrodes as the glycol deteriorates. This leads to leaks, so the coolant needs to be replaced regularly.
Battery Thermal Management Systems (BTMS) are costly to repair, have bulky piping, and are difficult to maintain.
The thermal components of a battery thermal management system also face challenges in the design and manufacturing process, including coolant selection, design of optimal flow paths, and simulation of complex system models.
All current quality and safety standards also need to be taken into account when designing a battery thermal management system.
To address these challenges, TKT has developed thermal management systems for
3KW-10KW batteries for electric buses, electric trucks, heavy equipment, etc. to solve these problems. Through coolant cooling and PTC heating, the temperature of the battery pack is kept within the right range to maintain a longer driving range and service life. TKT has the price advantage of mass production and the ability to supply to OEM customers worldwide.